Analytical Ferrography: Sample Preparation
In this article, we compare two different methods to prepare lubricant samples for analytical ferrography – the glass slide and filter patch techniques.
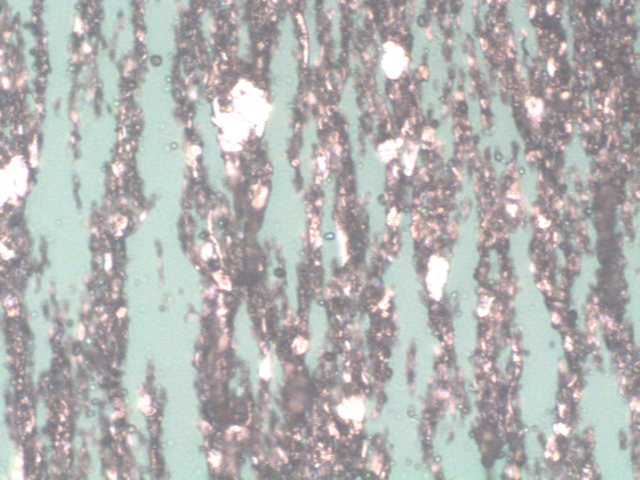
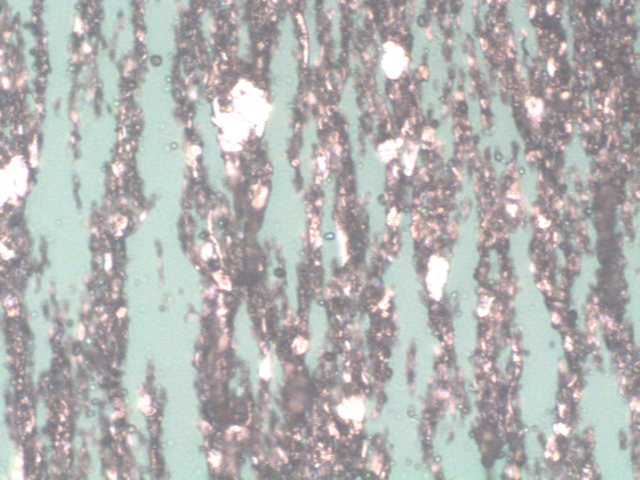
Analytical ferrography (microscopic analysis of a fluid sample) is an invaluable part in the oil analysis toolkit. By analyzing metallic particles present in used oil samples, under a microscope, you can often determine important information on the system such as wear severity, mode, and lubricated component location. Ferrography also allows the analyst to potentially identify contaminants in the oil such as dirt, fibers, or corrosion particles.
When preparing a sample of oil for ferrography, the analyst must deposit the wear particles, and other foreign materials, onto a substrate to then view them using a microscope.
The choice of substrate for the oil sample has a significant impact on the type of information that can be derived from the analysis.
Two main options exist for substrates: glass slides and filter patches.
Glass Slide
An example of a glass slide used in the preparation of ferrograms.
A glass substrate is a transparent, rectangular glass slide, with a U-shaped, oil-resistant barrier. The presence of the barrier allows for smooth flow of the oil sample down the slide and into a waste container. Prior to applying the oil sample, the slide is placed onto a ferrogram maker, which has a strong magnet underneath the slide aperture.
This magnet collects ferrous particles along its magnetic field lines, that separate ferrous vs. non-ferrous particulates. The presence of a slight slope on the slide aperture also allows for sorting of particles by size, with larger particles collecting near the mouth of the slide, and smaller particles near the end.
Filter Patch
An example of a filter patch membrane.
The filter patch consists of a very fine membrane, often with pores as small as 0.45 microns (10^-6 m) in size. This oil sample is mixed with a filtered solvent, such as heptane or petroleum spirits, and then poured through the filter membrane. The fine pores of the filter allow solvent and oil to pass but collect all particulates.
Glass Slide Microscopic Analysis
An example of a micrograph performed using a glass slide.
Advantages of using a glass substrate slide for microscopic analysis:
The glass slide is transparent
- The glass slide is transparent by nature, which assists in differentiating translucent/transparent particulates from those that are opaque. The presence of translucent, granular material is often an indicator of dirt contamination.
Heat resistance
- The heat resistant glass slide allows the use of a hot plate, most often set at 625F, to determine wear particulate metallurgy. Low alloy steel turns blue at this temperature, medium alloy steel turns bronze, while high alloy steel typically does not change color. Also, certain non-ferrous metals slightly melt at this temperature (Babbitt).
Separates particles by magnetism
- The magnet present on the ferrogram maker forces ferromagnetic particles (steel, dark oxides) to collect along magnetic field lines. This allows the analyst to easily differentiate between magnetic white metal particles and non-magnetic white metal particles (aluminum and some Babbitt materials).
Chemically resistant
- The chemical resistance of the glass slide can be extremely useful, as it allows the careful addition of alkaline or acidic mixtures onto the slide. This can assist in determination of metallurgy, or providing additional information on foreign materials present in the oil. For example, aluminum is a white metal, which does not change color after heating. This can make it difficult to differentiate between aluminum and high alloy steel, as high alloy steel often shows weak response to magnetic fields. However, aluminum reacts readily with potassium hydroxide (KOH), a common laboratory chemical, while high alloy steel does not.
Disadvantages of using the glass slide rather than the filter patch for analysis
Slower
- The preparation of the glass slide can take longer than a filter patch, due to setup, time for careful pipetting, and the wait for the solvent to dry. Devices exist to help automate these procedures, which helps to offset this inefficiency.
Non-magnetic particle loss
- Non-ferrous metals, dirt, and other non-magnetic particulates can be inadvertently rinsed off the slide, if the slide preparer is not cautious. This can lead to a lack of detection of these materials in the analysis stage.
Filter Patch Microscopic Analysis
An example of a micrograph performed using a filter patch.
Advantages of using a filter patch
Speed
- A filter patch can be prepared very quickly, as the main setup involves the preparation of the sample mixture. Often, a vacuum is used to quickly pull the sample mixture through the filter patch.
Retains non-magnetic particles
- Whereas the glass slide preparer must exercise caution to retain non-magnetic particulates, the filter patch collects all materials greater in size than the pore diameter.
Disadvantages of the filter patch
Not heat resistant
- The filter patch is often constructed from nitrocellulose or nylon, which are not tolerant of heat up the temperatures required to cause color changes in metal alloys. This means that the ferrographer can not easily determine wear particulate metallurgy.
No separation of particles by magnetic properties or size
- Because there is no magnet involved in the filter patch preparation, all particulates are deposited in random orientations. This makes it more difficult for the analyst to differentiate between metals such as steel and aluminum.
Opaque
- As the filter patch is made from an opaque material, it is not easy to determine if the visible particles are transparent/translucent. This makes it more difficult to identify debris such as red oxides or dirt.
As you can see, both options have merits.
Here at MRT, we generally prefer the use of a glass slide, but the filter patch technique is excellent in certain situations, such as when the primary focus of the analysis is on confirming the presence of non-magnetic particulates.
However, we feel that the ability to determine wear particle metallurgy, as well as the composition of certain foreign materials, are invaluable tools that help provide the maximum amount of information to our customers.
Please reach out to us if you have any additional questions regarding analytical ferrography, or other testing employed in oil analysis.
Ferrography is the best way to identify early-stage wear in your rotating equipment, but you must also pay attention to key fluid properties such as viscosity, flash point, and antioxidant health. Check out our test catalog for more info.
An experienced oil analysis professional is ready to help you get started testing.